Obtaining a device capable of manipulating objects electrically is a multifaceted process. It typically involves the selection of a suitable robotic gripper, designed for the specific task and load capacity. This selection might consider factors like the material being handled, the required force, and the precision needed. Detailed specifications of the device's electrical connections, power requirements, and control interface are crucial for integration into existing systems. The procurement process might encompass vendor selection, contractual agreements, and integration planning. Once acquired, the proper setup and calibration are vital for safe and effective performance.
The ability to manipulate objects using electrical means has profound implications. Increased productivity and safety are often realized. The potential for automation in hazardous or repetitive tasks is substantial. Automated handling of materials, especially in manufacturing and logistics, leads to reduced human error, minimized physical strain, and enhanced overall efficiency. This enables the development of more sophisticated, automated processes that further enhance productivity.
This discussion sets the stage for a more detailed exploration of robotic gripper selection criteria, electrical safety standards, and methods of integrating such devices into existing workflows. The following sections will address aspects of system design and optimization, considerations for maintenance and reliability, and the broader implications for industrial automation.
Obtaining Electric Grippers
Securing an electric gripper involves a systematic approach. Key considerations range from specifications to procurement and integration. Understanding these aspects is crucial for successful implementation.
- Specification
- Procurement
- Integration
- Calibration
- Maintenance
- Safety protocols
Selecting the appropriate gripper hinges on defining the intended task and load capacity. Procurement involves vendor research and evaluating quotes. Integration necessitates careful planning, considering electrical connections and control systems. Calibration ensures accurate performance. Maintenance schedules and procedures are vital for longevity. Rigorous safety protocols prevent accidents. Examples include using a specific gripper for delicate electronics assembly, or a more powerful gripper for heavy materials handling in manufacturing. These aspects, interwoven, guarantee the efficient and safe utilization of electric grippers in various applications.
1. Specification
Accurate specification is fundamental to obtaining the appropriate electric gripper. Precise definition of the required gripping force, load capacity, and material handling capabilities dictates the selection of the suitable device. A gripper intended for delicate components demands a different specification than one for heavy-duty materials handling. Failure to meticulously consider these factors can lead to the acquisition of a gripper unsuitable for the task, resulting in inefficiencies or potential damage. For instance, attempting to handle a heavy metal plate with a gripper designed for fragile electronic components could lead to a catastrophic failure. Conversely, employing a robust gripper for a light assembly operation results in unnecessary expenditure and operational complexity.
Specifications encompass more than just the physical dimensions and weight capacity of the electric gripper. Critical details include the electrical interface, control protocols, power consumption, and data communication methods. Discrepancies in these areas can impede integration with existing systems. For example, a gripper with incompatible communication protocols would require costly modification or replacement of the entire control system. Thorough understanding of these specifications is paramount for efficient integration and cost-effectiveness. Proper analysis allows for informed procurement decisions, minimizing the risk of encountering compatibility issues down the line.
In summary, meticulous specification acts as a crucial cornerstone in the process of acquiring an electric gripper. Precise definition of operational requirements is essential to obtaining a suitable device, avoiding costly mismatches, and ensuring successful integration within existing systems. Neglecting these specifications can lead to significant challenges, from operational inefficiency to costly rework or replacement. The importance of thorough analysis and careful specification should be paramount to stakeholders throughout the procurement process.
2. Procurement
Procurement, as a critical component of obtaining an electric gripper, encompasses the process of acquiring the device. This process necessitates a systematic approach, encompassing vendor identification, evaluation, negotiation, contracting, and ultimately, delivery. Failure to execute these steps effectively can impede the acquisition process, leading to delays, increased costs, and potentially inappropriate equipment. For instance, selecting a vendor without adequately assessing their production capabilities, delivery timelines, or product warranties can result in substantial disruptions to project timelines and budgets.
The importance of robust procurement procedures lies in their ability to ensure the acquisition of high-quality, reliable equipment. Thorough due diligence during the vendor selection phase, including examination of past performance and client testimonials, minimizes the risk of receiving faulty or poorly maintained equipment. Furthermore, rigorous contract negotiation guarantees favourable terms, addressing issues like warranty periods, maintenance agreements, and future support obligations. A company deploying electric grippers for a complex assembly line requires a robust procurement strategy to guarantee a dependable supply chain and prevent unexpected downtime. This includes considering factors like lead times, potential disruptions due to unforeseen events, and the need for alternative suppliers. Practical experience demonstrates that well-defined procurement procedures can significantly improve the long-term operational efficiency of businesses.
In conclusion, procurement stands as a pivotal aspect of obtaining an electric gripper. A well-structured process safeguards against risks, ensures quality, and reduces potential disruptions to production. Rigorous analysis, clear contract specifications, and robust supplier relationships underpin successful procurement and ultimately contribute to a streamlined approach to acquiring and integrating electric grippers into production processes.
3. Integration
Successful integration of an electric gripper is critical to its effective use. The process of seamlessly incorporating this technology into existing workflows necessitates careful planning, technical expertise, and a thorough understanding of both the gripper's capabilities and the surrounding system. Without meticulous integration, the gripper remains a standalone component, failing to realize its potential benefits in automation and efficiency.
- Electrical Compatibility and Control Systems
Ensuring the gripper's electrical specifications align with the existing power distribution and control systems is paramount. Incompatible voltage, current, or communication protocols can lead to malfunctions or damage. Thorough testing and validation of compatibility are essential. Examples include using appropriate power supplies, verifying data communication protocols, and adapting control signals. This minimizes the risk of damage to the gripper and the connected machinery, crucial for safe and efficient operation. Failure to address these compatibility issues can lead to disruptions in production and costly repairs.
- Mechanical Integration and Workspace Design
The gripper's physical dimensions and operating requirements must be considered in the workspace design. Adequate clearance, ergonomic positioning, and suitable mounting mechanisms are crucial. For example, ensuring the gripper's reach encompasses the required work area and avoiding interference with existing equipment is essential. Inadequate workspace planning can lead to collisions or restricted movement, negatively impacting the gripper's operational efficiency and safety.
- Software Integration and Programming
The integration process extends to software. The gripper's control software needs to seamlessly interact with the existing automation software or control systems. Programming for tasks, including motion control, gripping force adjustments, and data feedback loops, needs to be performed accurately. Proper programming ensures smooth and efficient execution of the gripper's tasks within the larger automation scheme. Errors in programming can result in incorrect operation, causing material damage or equipment malfunction.
Effective integration is not a passive process; it requires a comprehensive understanding of the gripper and the existing system. By considering the interplay between electrical and mechanical components, as well as software programming, a company can avoid disruptions to the automation process, realize anticipated benefits of the electric gripper, and maintain a safe and productive workflow. Each facetelectrical compatibility, workspace design, and software integrationplays a crucial role in realizing the full potential of the electric gripper.
4. Calibration
Calibration of an electric gripper is an essential component of its effective operation. Precise calibration ensures accurate and reliable performance, minimizing errors and maximizing the gripper's efficiency. Without proper calibration, the gripper may misjudge gripping force, leading to damage to the workpiece or the gripper itself. In applications requiring precision, such as handling delicate electronic components, inaccuracies introduced by miscalibration could result in significant product defects or even equipment damage. Examples include precise assembly tasks in electronics manufacturing, where a poorly calibrated gripper could damage or misplace small parts, leading to costly rework or scrap.
Calibration procedures typically involve establishing a baseline for the gripper's performance. This process often involves standardized test items with known dimensions and weights. Measurements are taken to determine the gripper's actual force output and accuracy. Adjustments are made to the gripper's control parameters until the desired performance is achieved. This iterative process ensures consistent and predictable gripping force, preventing inconsistencies and variations that can impact production output. In material handling applications, accurate calibration is paramount to ensuring optimal gripping pressure for different materials, preventing damage or slippage. For example, a gripper handling fragile glass products requires precise calibration to avoid breaking the items and preventing damage to the gripper jaws.
Accurate calibration significantly contributes to the overall reliability and safety of the system. It minimizes the risk of errors, ensures predictable performance, and ultimately reduces the potential for downtime and damage. The importance of calibration extends to the broader application of electric grippers, emphasizing its integral role in achieving optimal efficiency and safety in automation processes. Companies with strict quality control requirements will often employ rigorous calibration protocols to meet industry standards and maintain high-quality products. The value proposition of precise calibration, therefore, lies in maximizing efficiency and minimizing errors, ultimately leading to a higher return on investment by reducing the costs of rework, maintenance, and potential damage.
5. Maintenance
Effective maintenance is inextricably linked to the optimal operational lifespan of an electric gripper. Proper maintenance procedures directly influence the reliability, safety, and overall performance of the device. Neglecting maintenance can lead to premature failure, increased downtime, and substantial repair costs. Regular upkeep encompasses a range of activities, from routine inspections to more extensive servicing, all contributing to the long-term operational integrity of the gripper. For instance, a manufacturing facility relying on electric grippers for automated assembly will experience significant productivity losses if equipment malfunctions due to inadequate maintenance.
Essential maintenance activities include regular lubrication of moving parts, ensuring smooth operation and minimizing wear. Inspection for signs of damage or wear, such as frayed cables, bent joints, or loose connections, is vital. Prompt identification and repair of any anomalies prevent escalating issues. Moreover, periodic cleaning, particularly in environments with contaminants, preserves the gripper's functionality and extends its lifespan. Regular calibration, to ensure consistent gripping force and accuracy, also falls under the umbrella of maintenance. Failure to maintain calibration can lead to inconsistencies in assembly processes, impacting product quality and potentially causing equipment damage. Real-world examples abound: a hospital using a robotic gripper for surgical procedures needs meticulous maintenance to ensure the precision and sterility required for patient safety, avoiding malfunctions during critical operations.
In summary, a proactive maintenance strategy is integral to the long-term success and safety of electric gripper implementation. Neglecting scheduled maintenance can result in substantial costs associated with repairs, lost production time, and potential safety hazards. Understanding and adhering to the specific maintenance requirements outlined by the manufacturer are essential to ensure the sustained reliable operation of the electric gripper. The benefits of a comprehensive maintenance program, therefore, extend beyond operational efficiency and include the assurance of a safe, predictable, and cost-effective workflow. By proactively addressing potential issues through scheduled maintenance, organizations can minimize the risk of unexpected downtime and maximize the return on investment in electric gripper technology.
6. Safety Protocols
Safety protocols are an integral component of the process for obtaining and operating an electric gripper. Failure to adhere to these protocols can lead to serious injury, equipment damage, and disruptions in production. Essential safety protocols must be integrated from the outset of the selection process, through procurement, integration, and ongoing operation. This includes comprehensive risk assessments, adhering to industry safety standards, and establishing clear emergency procedures.
Effective safety protocols encompass a range of measures. These include, but are not limited to, rigorous electrical safety standards, ensuring proper grounding and insulation of all electrical components. Equipment operators need thorough training on the safe operation of the electric gripper, including proper use of safety devices, such as emergency stops. The workspace environment itself plays a crucial role; ensuring proper illumination, unobstructed access, and clear signage, especially in potentially hazardous areas, can prevent accidents. Detailed procedures must be in place for handling malfunctions, including immediate shut-down protocols and emergency response procedures. For instance, in a manufacturing setting involving heavy machinery and high-velocity materials, safety protocols are critical to prevent injuries from collisions or entanglement. Detailed emergency shutdown plans should be reviewed regularly and updated to reflect changing operational demands.
Properly implemented safety protocols minimize the risk of accidents, protect personnel, and safeguard equipment. A thorough understanding of safety protocols is essential for the successful acquisition and utilization of electric grippers. Adherence to industry standards and comprehensive safety procedures minimizes risks associated with electrical hazards, mechanical failures, and operator error, leading to a safer and more productive work environment. Ultimately, a strong emphasis on safety is crucial for mitigating potential harm, ensuring successful implementation of automated systems, and maintaining a positive return on investment in the technology. Failure to prioritize safety can have severe consequences in terms of financial losses, legal ramifications, and workplace injuries.
Frequently Asked Questions
This section addresses common queries regarding the process of acquiring and implementing electric grippers. Clear and concise answers aim to provide comprehensive insight.
Question 1: What factors should be considered when selecting an electric gripper?
Selection hinges on the specific task. Key factors include load capacity, gripping force requirements, material compatibility, and the workspace environment. Assessing these factors allows for selection of a suitable device for the intended application, preventing inefficiencies or potential damage.
Question 2: What are the critical elements in the procurement process?
The procurement process encompasses vendor identification, evaluation, contract negotiation, and delivery. Rigorous evaluation of vendor capabilities, timelines, and warranties is essential to ensure quality and timely delivery of the electric gripper. Comprehensive contract negotiation, addressing issues like maintenance and support, protects both parties.
Question 3: How can the integration process be optimized?
Optimization necessitates careful planning regarding electrical compatibility, mechanical integration, and software interfaces. Ensuring compatibility with existing power and control systems, proper workspace design, and seamless integration with existing automation software are crucial for a smooth transition. Testing and validation throughout the integration phase are vital.
Question 4: What maintenance procedures are essential for electric grippers?
Regular lubrication, inspections for damage, and periodic cleaning are critical. Adherence to manufacturer-specified maintenance schedules and procedures ensures optimal operational lifespan and prevents premature failure. Proper calibration procedures are also part of a comprehensive maintenance program.
Question 5: How can safety be prioritized in the use of electric grippers?
Adherence to safety protocols, including electrical safety standards, operator training, and well-defined emergency procedures, is crucial. Rigorous risk assessments, incorporating safety measures throughout the operation, reduce the likelihood of accidents and equipment damage. Compliance with industry standards minimizes risk.
Question 6: What are the long-term implications of not addressing these factors effectively?
Neglecting appropriate selection, procurement, integration, calibration, maintenance, and safety protocols leads to increased operational costs. This includes potential equipment damage, safety hazards, costly repairs, and ultimately, reduced productivity and efficiency. Failure to address these elements can result in significant operational disruptions.
In conclusion, careful consideration of each stage in the acquisition and implementation of electric grippers significantly contributes to a smooth transition and successful outcomes. Understanding these factors is vital for realizing the full potential of automated systems.
The subsequent sections will delve into detailed aspects of system design and optimization.
Tips for Acquiring and Implementing Electric Grippers
Effective acquisition and implementation of electric grippers hinge on careful planning and execution. These tips offer a structured approach, encompassing crucial aspects from initial selection to ongoing operation. Adherence to these recommendations ensures successful integration and optimal return on investment.
Tip 1: Define Specific Requirements.
Clear articulation of the task is paramount. Precisely defining the intended application, including the weight and type of objects to be manipulated, gripping force needed, and environmental conditions, is crucial. An assembly line requiring delicate component handling necessitates different specifications than a system for heavy materials handling. Failure to accurately define these requirements can lead to mismatched equipment and inefficiencies.
Tip 2: Conduct Thorough Vendor Research.
Identifying and evaluating potential suppliers is essential. Assessment of a vendor's production capabilities, delivery schedules, warranty provisions, and past performance is vital. Reference checks and analysis of client testimonials can inform a reasoned choice. Prioritizing vendors with demonstrable expertise in providing equipment for similar applications can contribute to the success of the project.
Tip 3: Develop Comprehensive Integration Plans.
Integrating the electric gripper into existing systems requires careful planning. Assessing electrical compatibility, mechanical interface requirements, and software integration needs is critical. Ensuring the gripper's specifications align with existing systems minimizes potential disruptions and complications during implementation. This proactive approach reduces installation time and costs.
Tip 4: Implement Rigorous Calibration Procedures.
Calibration procedures are vital for maintaining accuracy and consistency in gripping performance. Standardized test items are helpful for establishing baseline performance metrics and enabling adjustments to ensure precise force output. Regular calibration ensures reliable operation, prevents equipment damage, and helps maintain product quality, especially in applications requiring precision.
Tip 5: Establish Proactive Maintenance Schedules.
Proactive maintenance, encompassing routine lubrication and inspections, is crucial for optimal long-term performance. Adherence to manufacturer-recommended schedules ensures timely detection and resolution of potential issues. This approach minimizes equipment downtime and maximizes the operational lifespan of the electric gripper.
Tip 6: Implement Robust Safety Protocols.
Implementing rigorous safety protocols throughout the entire process is paramount. These protocols must address electrical safety, operator training, and emergency procedures. Thorough risk assessments and compliance with safety standards mitigate potential hazards. Adhering to established industry standards enhances safety and mitigates liability.
By strategically applying these tips, organizations can navigate the acquisition and implementation of electric grippers more effectively, ensuring operational efficiency, minimizing potential issues, and maximizing the return on investment. These principles guide a more streamlined approach to automation processes, enabling greater efficiency and productivity.
The subsequent sections will address more detailed aspects of system design and optimization.
Conclusion
Acquisition and implementation of electric grippers necessitate a systematic approach encompassing meticulous specification, robust procurement, seamless integration, precise calibration, proactive maintenance, and rigorous safety protocols. Successful deployment hinges on a thorough understanding of the specific application, encompassing load capacity, material types, and operating environment. Effective vendor selection and contract negotiation are crucial for securing reliable equipment and favorable terms. Integration demands careful planning and execution to avoid complications, ensuring compatibility with existing infrastructure. Precise calibration and scheduled maintenance routines safeguard equipment lifespan and consistency. Prioritizing safety protocols throughout the entire process mitigates risks and protects personnel. This comprehensive framework ultimately ensures successful operation and return on investment. Failure to adequately address these interconnected elements can lead to substantial operational disruptions, increased costs, and safety hazards.
The acquisition of electric grippers represents a significant step towards automation and efficiency. This technology holds considerable potential for productivity improvements, cost reduction, and enhanced safety, particularly in demanding industrial settings. Continued exploration of innovative applications, advancements in gripper technology, and sustained emphasis on safety protocols will ensure the continued growth and adoption of these sophisticated tools across various sectors. Organizations should adopt a proactive approach toward implementing and integrating electric gripper systems, ensuring that the benefits of this technology are fully realized within the context of operational efficiency and risk mitigation.
You Might Also Like
Vignesh Shivan Age - [Year Of Birth]Charming Jack Sock Wife: Cozy Comfort Style
Rachel Reynolds Wiki - Bio, Facts & More
SpongeBob SquarePants Net Worth: How Rich Is He?
Chrissy & Mr. Jones Net Worth: 2024 Update
Article Recommendations
- Ron Palillo Net Worth 2024 A Deep Dive
- Top Megan Fox Pics Unforgettable Looks
- Expecting A Baby Ashantis Pregnancy Journey
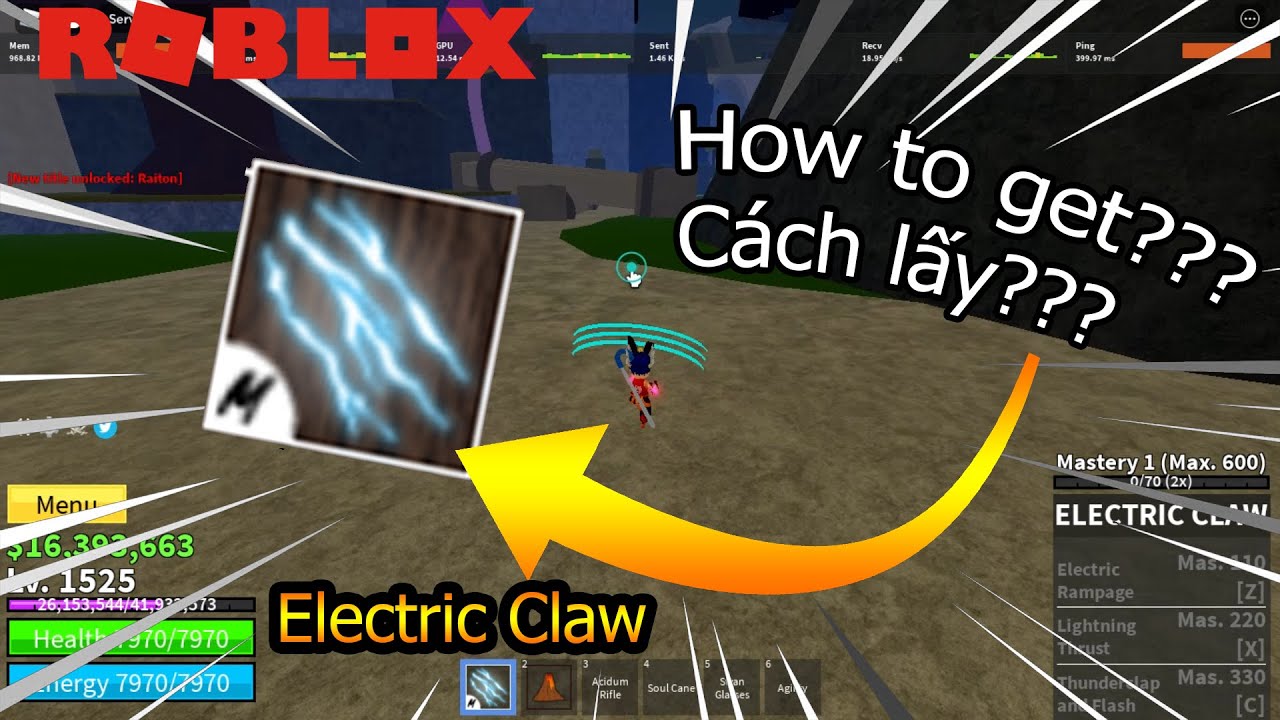
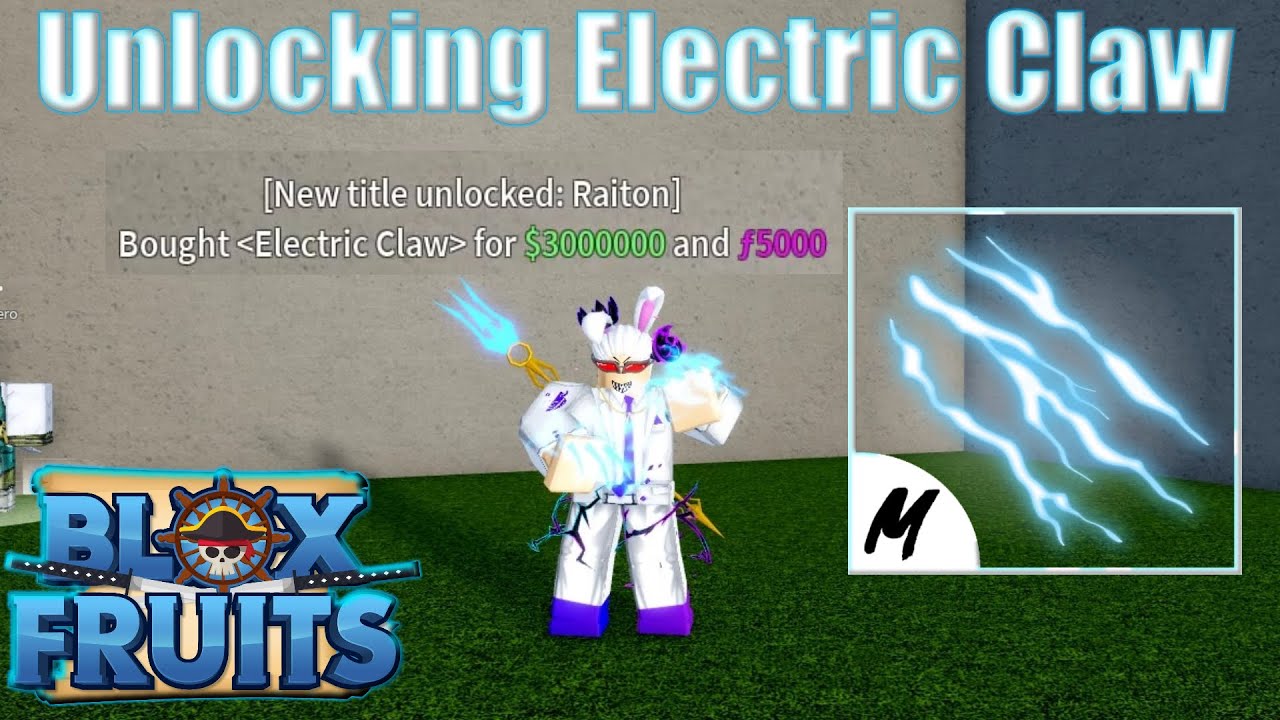
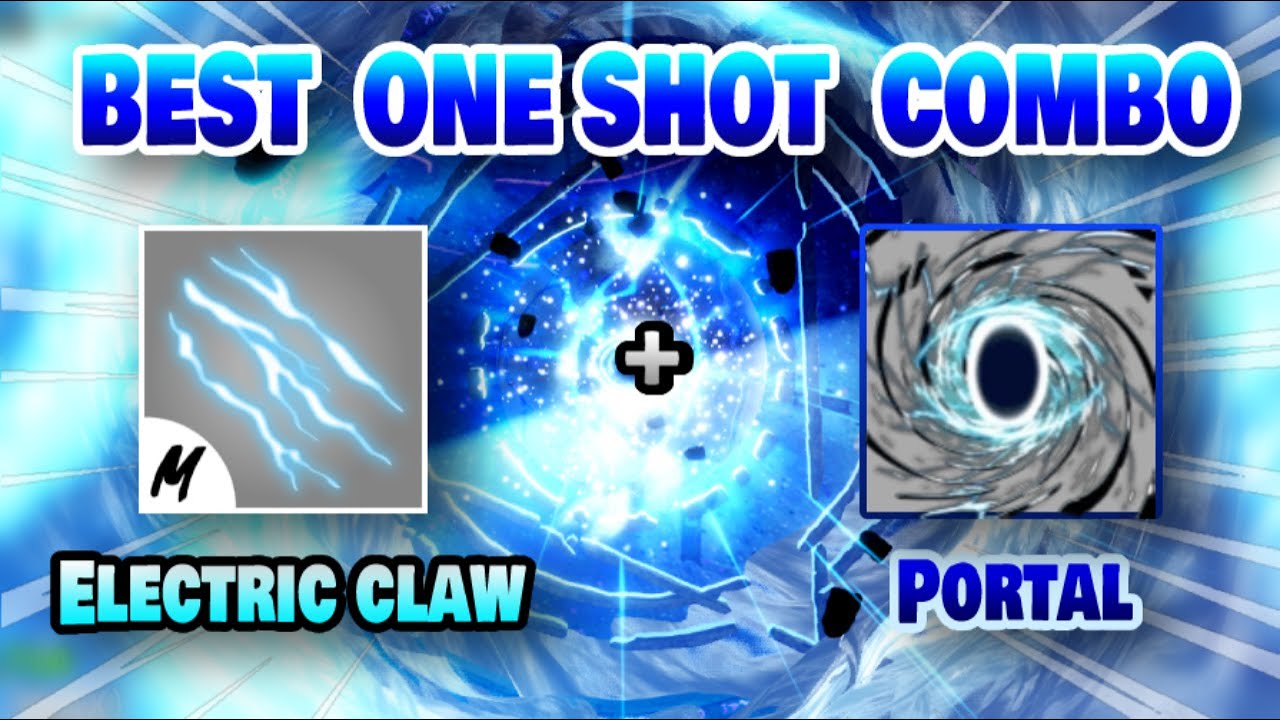